1
HOME > Cars >
THE DIFFERENT TYPES OF ALLOY WHEELS
Written by Menswear Style in Cars on the 12th February 2021
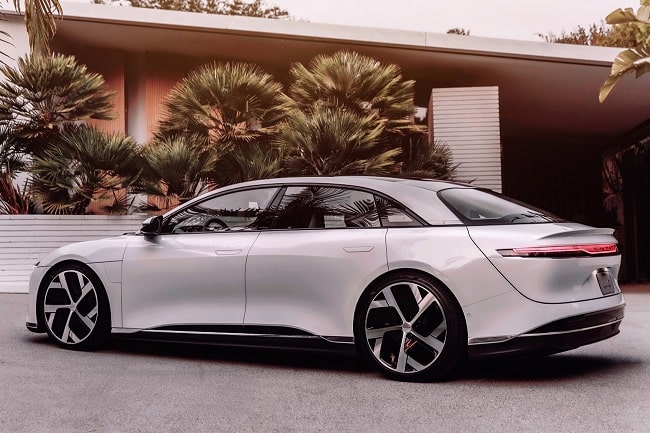
Alloy wheels are popularly used in automotive cars because they’re known for their durability and their capacity to be aesthetically enhanced. They are made up of various metals, commonly, aluminium or magnesium. Steel can be considered as alloy but, particularly, alloy wheels cover those that are made from non-ferrous metals. There are different types of alloy wheels and choosing the right one for your needs can considerably aid in providing you that superb driving experience. Here are some of them:
Aluminium Wheels
These are the most popular among alloy wheels, they’re made with a blend of aluminium and nickel. While steel wheels are made from an alloy of iron and carbon, which makes them more durable, they are heavier and don’t offer a wide range of aesthetic opportunities. Notably, the people from Advantage Alloy Repairs says that wheels made from aluminium are lighter than their ferrous counterparts. These properties contribute to a car’s fuel economy as well as its performance and handling. They are also resistant to corrosion which meets the arduous demands of a car’s component that gets the most brunt.
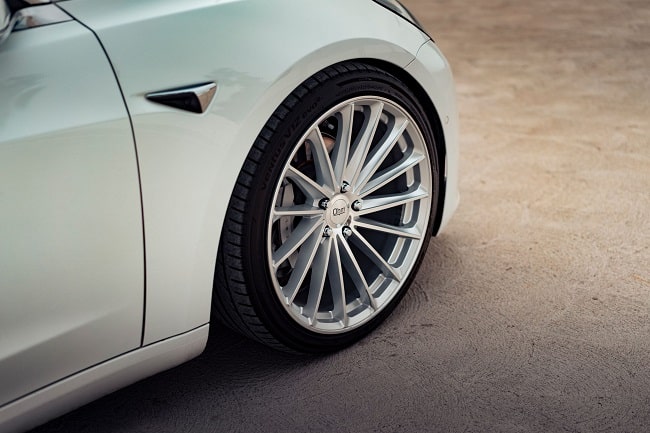
Mag Wheels
These are wheels made from magnesium instead of aluminium and were originally used for race cars prior to its fame in standard production. They are lighter than aluminium wheels which made them widely used in racing circuits. They also have the looks which make them commonly used as aftermarket wheels that will definitely make you stand out. However, they are slightly more expensive than aluminium wheels and when they bend, it’s almost impossible to straighten them out. Originally, they were susceptible to corrosion and damages, but engineers found a way to correct some of its downsides through die-casting.
Die Casting Wheels
There are two major processes in making alloy wheels namely, low-pressure die casting and high-pressure die casting. The former involves forcing molten alloy materials into the die using pressurised air. This method allows the metal to cool down and harden to a certain point and makes them stronger and more docile. It increases their resistance to changing pressure and heat. High-pressure die casting works similarly, but the die is sealed with great pressure. It is the more economical process without foregoing its corrosion-resistive attributes, and it also allows designers to create more intricate designs than low-pressure die casting.

Forged Wheels
While die casting uses moulds to form the molten alloy material to form the wheel, forged wheels are made from a single aluminium that is heated to allow machines to apply the designs. It may sound simple, but the process involves rolling, heating, applying pressure, and hammering which takes more time and energy to accomplish. This type of alloy wheels is used by performance vehicles and top-tier models because they are very costly to make. The advantages however are wheels that are three times stronger and a quarter lighter than standard alloy wheels.
Multi-piece Alloy Wheels
This method takes two or three separate pieces and combines them to create a single wheel. The hub can be forged or cast while the rims are normally spun from a disk of aluminium. Together they are bolted and then a sealant is applied. They are popularly used on 17” wheels with each section given the special custom-made tailoring for aesthetic purposes. There is no doubt that alloy wheels are king when it comes to wheel performance and design. Engineers use technology derived from racing, and with a little ingenuity, have introduced it to standard production which has elevated the driving experience of the modern driver.
Trending
2
3
4
5
6
7
8
9
10